The Corona pandemic has not passed the trade sector without leaving its mark. Many companies were forced to switch to eCommerce and market their products online. According to a study by Rakuten Advertising that 65 % of all Germans will buy products online during the Christmas shopping season - almost 48 % of them from their mobile device. While in France and England, for example, people are saving significantly more than before, around 85 % of all Germans are not planning to cut their Christmas shopping budget. After a bumpy year, retailers have prospects for particularly high sales in the fourth and final quarter.
With the expected increase in orders, starting with the Black Friday to Cyber Monday period (BFCM), it is high time to also adapt your inventory management to the rising propensity to buy. Warehousing1 presents here the most important points that your eCommerce shop should consider with regard to inventory management for the pre-Christmas period.
The importance of a functioning inventory management
The main goals in any inventory management is on identifying and managing critical stocks. Delivery risks should also be completely avoided. With a tight cash flow, companies must carefully consider which stock can be purchased, which in the end will not only stay on the shelves but will also be sold again quickly. For inventory planning, the so-called abc-analysis is therefore often used. This method determines the value of the individual stock items for the company - from A (generating the most sales) to C (generating the least sales).
This classification of stocks is mostly done manually. The remedy is innovative systems that give you insight into your stock levels at any time. Dynamically optimised inventories enable you to use your financial resources in inventory planning exactly where they are needed most at the moment. At the same time, you can keep stock levels as low as possible and avoid overstocking. With Warehousing1, you also always have an overview of the most important warehouse data on our central dashboard, which gives you flexible room to manoeuvre.
Christmas time is time to take inventory
Especially towards the end of the year, it is important to determine the actual stock level or the number of products and goods. At the latest after the Christmas business, your stocks should be back at a regular level. Stocktaking itself means a recording of all stocks as well as assets on a certain date. The determination and counting of products and goods is usually associated with high personnel costs, which is why prior planning is essential. Inventories are legally anchored in the principles of proper accounting (GoBD) and form the basis for your annual financial statements.
In general, the following three types of inventories can be distinguished: Three types of inventories for inventory planning:
- Key date inventory: 10 days before or after the balance sheet date; on the day of the inventory a complete inventory has to be made
- Permanent inventory: step-by-step; e.g. monthly determination of the inventory of a certain product group
- Sample inventory: for large companies that list more than 1,000 items, provided that 20% of the goods represent 80% of the turnover or electronic stock accounting is used; this type of inventory must be approved by the responsible tax office
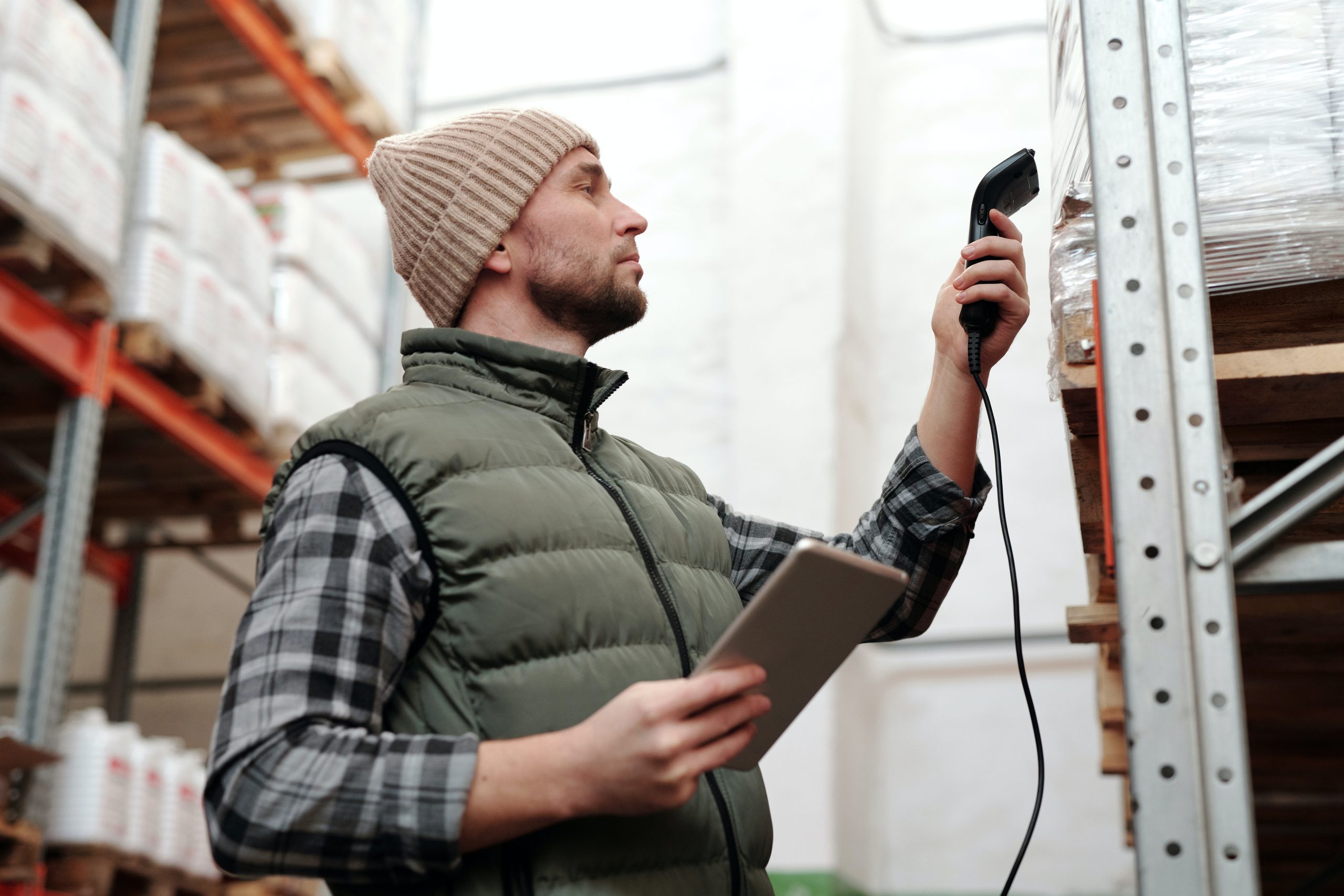
Traders who already make use of technical aids for their stock inventories have a clear advantage over their competitors, as they can usually also register a clear time saving. Stocktaking after Christmas enables your warehouse to clean up any shortages or surpluses accumulated over the year and to determine the actual value of goods in the warehouse. Afterwards, you can easily determine inventory-related Key Performance Indicators (KPIs) to analyse your overall performance in inventory management. You can find an overview of the most important warehouse KPIs here. hereThus you create the best conditions for your warehouse to start the new business year top organized and well positioned.
Be prepared for delays in delivery
The area of logistics represents one of the main pillars of customer satisfaction. In times like these, however, logistics in particular is more sensitive than ever before. This is mainly because it requires the physical presence of employees to handle fulfilment as well as shipping. Due to government regulations, logistics service providers around the world have had to adapt their human resources management and implement measures to ensure the health of their employees. This can lead to restrictions in operational activities, which should of course be prevented at all costs.
Especially around Christmas, delivery delays represent an enormous risk to succeed in your business. Due to the pandemic, Apple, for example, postponed the launch of the iPhone 12 to October 13 and has delayed the shipping of the Mini and Pro Max models even more. But it is not as simple as that with the Christmas holidays. The Corona crisis has achieved one thing above all: It has shown that adjustments to the supply chain should be made on a regular basis.
So that you too are prepared for the holidays, it makes sense to reduce the otherwise relatively high turnover rate. This means that the stock in the warehouse should be increased in order to avoid stock-outs. Also contact your suppliers directly to clarify whether deliveries can be blocked so that all gifts arrive in time for the holidays.
More insights and helpful tips about necessary holiday preparations can be found in our new eBook "The Warehousing1 eCommerce guide for the Christmas & holiday business". Enclosed to the eBook you will also find two practical checklists that will help you prepare your logistics for all eventualities. If you have any questions about our services or want to get started with WH1 right away, simply book your appointment for a personal consultation with one of our account managers. We look forward to hearing from you!